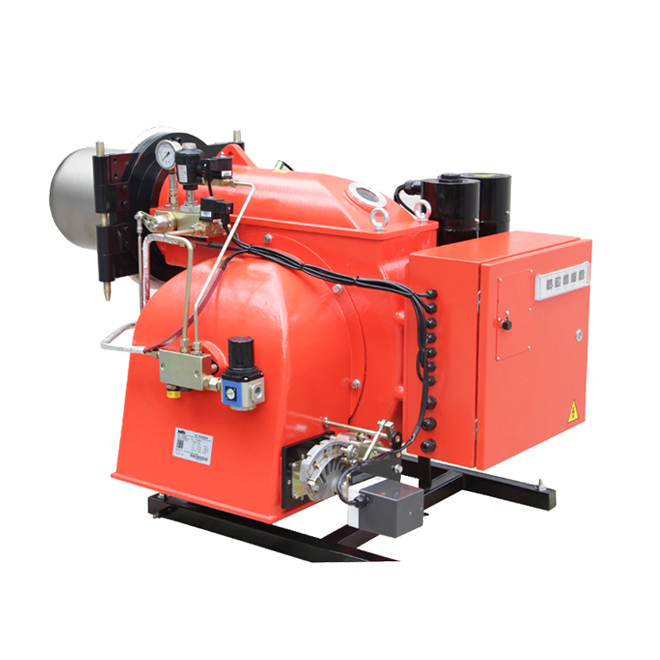
There are two main combustion methods for gas boilers. One is the special burning method, that is, the boiler is only equipped with a gas combustion system. At this time, the advantages of the gas boiler in terms of equipment investment and operating economy can be fully reflected; the other is It is a mixed combustion method, equipped with two combustion systems: gas-oil and gas-coal. The boiler can burn coal gas alone or burn another fuel alone or mix the two fuels. At this time, it is also called a dual-fuel burner. The dual fuel burner is the same burner with both gas nozzle and fuel nozzle. The air regulator, burner stabilizer, ignition device and flame monitoring device of the control part of the dual-fuel burner must be suitable for both fuels.
Composition structure: The dual-material burner is mainly composed of three parts: common parts, fuel parts, and gas parts. Common components: common components include air pipes, guide vanes used to control the air flow, air branch pipes and refractory fire channels. In addition, there must be a small fire igniter, and its location should be able to reliably position both fuel and gas. The position of the flame detector should be able to detect small fires, main gas flames and fuel (or coal) flames. Installing a much larger gas supply system in the oil burner may interfere with the mixing method of oil combustion. The solution is to arrange the gas inlet outward to the periphery of the burner.
Fuel components: mainly oil atomizers. Its function is to make the oil flow separate and distribute the oil mist into the air flow in a controllable manner. The commonly used atomizers are as follows:
1. Jet atomizer
The oil enters the swirling chamber through the orifice on the corner, and then sprays out from the ring nozzle in the shape of a cone, and is dispersed into droplets. The oil pressure is usually 0.35 to 1.4 MPa, up to 7.5 MPa. The viscosity of the oil under the best working condition is about 15×1030 m2/sec. A simple jet atomizer often affects the load regulation ratio of the burner, but it can be improved by using overflow reflux. Because the excess oil can be refluxed, the amount of oil entering the swirl chamber is always constant regardless of the flow rate: a good swirl flow can be formed when the flow rate is large, and a certain thickness of oil mist flow can be maintained at the outlet when the flow rate is small.
2. Steam spray-assisted atomizer
This is an early atomizer used. The steam is led into the oil stream, and the oil is broken into mist due to impact. Due to the high steam consumption, when the jet atomizer appeared, this atomizer lost its attractiveness. In recent years, major reforms have been made to this type, which greatly reduces steam consumption.
Gas components
Without exception, the gas components of the dual-fuel burner adopt the nozzle orifice mixing type. The oil atomizer occupies the center of the burner stabilization zone, so the gas components are subject to certain restrictions. Using a detachable nozzle or ring cavity for heating can make it reach the center; but it cannot be used in combination with a rotary cup oil atomizer. In other design styles, as the load increases, the center supply Qi also becomes difficult. Therefore, as mentioned above, the gas is generally introduced through a ring or nozzle between the atomizer and the housing.
Classification
Dual-fuel burners can be divided into two categories: assembled burners (including fans and control devices, which are assembled by the manufacturer before leaving the factory) and field assembled burners (burners and controllers are assembled on site, Additional fan). The former is mostly used in fire tube boilers, and the latter is often used in water tube boilers. Generally speaking, dual-fuel burners are developed around existing oil burners. An oil atomizer has been installed on the center line of the burner. Gas must be introduced from the space between the oil atomizer and the housing.
Composition structure: The dual-material burner is mainly composed of three parts: common parts, fuel parts, and gas parts. Common components: common components include air pipes, guide vanes used to control the air flow, air branch pipes and refractory fire channels. In addition, there must be a small fire igniter, and its location should be able to reliably position both fuel and gas. The position of the flame detector should be able to detect small fires, main gas flames and fuel (or coal) flames. Installing a much larger gas supply system in the oil burner may interfere with the mixing method of oil combustion. The solution is to arrange the gas inlet outward to the periphery of the burner.
Fuel components: mainly oil atomizers. Its function is to make the oil flow separate and distribute the oil mist into the air flow in a controllable manner. The commonly used atomizers are as follows:
1. Jet atomizer
The oil enters the swirling chamber through the orifice on the corner, and then sprays out from the ring nozzle in the shape of a cone, and is dispersed into droplets. The oil pressure is usually 0.35 to 1.4 MPa, up to 7.5 MPa. The viscosity of the oil under the best working condition is about 15×1030 m2/sec. A simple jet atomizer often affects the load regulation ratio of the burner, but it can be improved by using overflow reflux. Because the excess oil can be refluxed, the amount of oil entering the swirl chamber is always constant regardless of the flow rate: a good swirl flow can be formed when the flow rate is large, and a certain thickness of oil mist flow can be maintained at the outlet when the flow rate is small.
2. Steam spray-assisted atomizer
This is an early atomizer used. The steam is led into the oil stream, and the oil is broken into mist due to impact. Due to the high steam consumption, when the jet atomizer appeared, this atomizer lost its attractiveness. In recent years, major reforms have been made to this type, which greatly reduces steam consumption.
Gas components
Without exception, the gas components of the dual-fuel burner adopt the nozzle orifice mixing type. The oil atomizer occupies the center of the burner stabilization zone, so the gas components are subject to certain restrictions. Using a detachable nozzle or ring cavity for heating can make it reach the center; but it cannot be used in combination with a rotary cup oil atomizer. In other design styles, as the load increases, the center supply Qi also becomes difficult. Therefore, as mentioned above, the gas is generally introduced through a ring or nozzle between the atomizer and the housing.
Classification
Dual-fuel burners can be divided into two categories: assembled burners (including fans and control devices, which are assembled by the manufacturer before leaving the factory) and field assembled burners (burners and controllers are assembled on site, Additional fan). The former is mostly used in fire tube boilers, and the latter is often used in water tube boilers. Generally speaking, dual-fuel burners are developed around existing oil burners. An oil atomizer has been installed on the center line of the burner. Gas must be introduced from the space between the oil atomizer and the housing.