Design requirements and process characteristics of Biomass and gas Multichannel Burner
The heat of rotary kiln is provided by the burner of rotary kiln. The burner plays a very important role in the calcining process of rotary kiln. It not only provides fuel and oxidant for combustion, but also is the main power unit of flame molding.
Foreign cement burners really began to develop in the 1970s, with the first generation of three-channel burners developed by France Pillard Company as the starting point.In fact, there have been dual-channel coal burners that mimic fuel burners before, but due to the lack of scientific research on pulverized coal combustion and gas-solid power and the improper operation parameters, the effect is not ideal in industrial production.The emergence of Pillard three-channel burner not only replaces the backward single-channel burner (i.e. coal jet), but also officially marks the research of cement burner into people's sight.
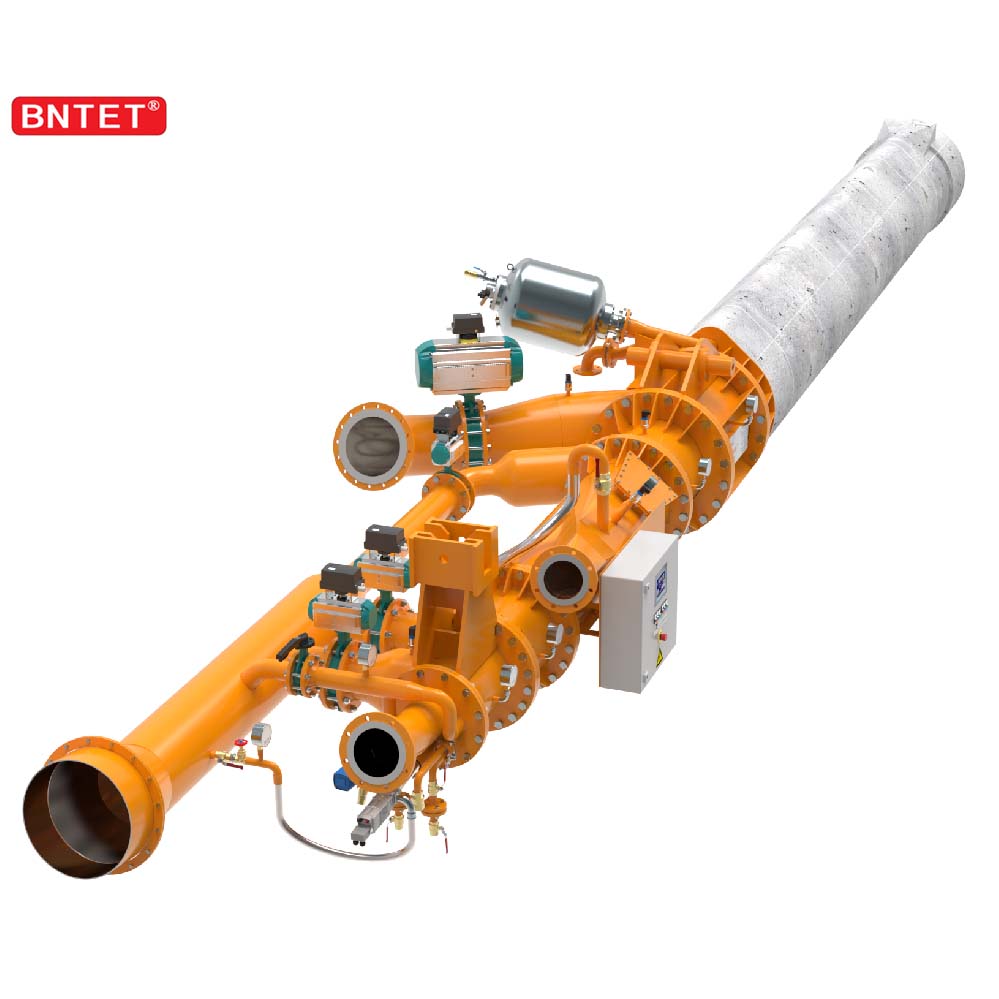
Design requirements for Biomass and gas Multichannel Burner:
1. Strong adaptability to pulverized coal quality.
2, the shape of the flame is thin but not long, so that the whole burning zone has a strong and uniform heat radiation.
3, the primary air volume as little as possible, but must ensure the stability of flame combustion in abnormal kiln conditions.
The technological characteristics of the Biomass and gas Multichannel Burner:
1. It has a good flame shape and reduces the peak temperature of the flame, and the heat flow distribution is good.
2. By reducing primary air volume by 4% and replacing it with high-temperature reflux flue gas (700-1100℃), fuel combustion is more complete, saving about 1.5% of fuel.
3. Simplify the flame shape adjustment process and expand the scope of adjustment.
4. due to the reduction of the flame temperature peak and the increase of high-temperature reflux flue gas, the NOX production has been greatly reduced.
Working principle and history of Biomass and gas Multichannel Burner
The commonly used fuels for rotary kiln burners are pulverized coal, gas, natural gas and heavy oil.
Generally according to the process requirements, local resources and supply conditions to choose.
When using pulverized coal as fuel, because the silica in coal will pollute the product, kilns that have strict requirements on product quality, such as alumina calcination kilns, carbon kilns and some heavy nonferrous metallurgy kilns, cannot use pulverized coal.
The adjustment of gas is more flexible, but if in the factory specially built gas station to produce gas, the investment is too high.If producer gas is used, the flame temperature is controlled.Some small external heat kilns (rotary tubes) are heated by electric wires.According to the rotary kiln used by the different fuel selection of the corresponding burner.