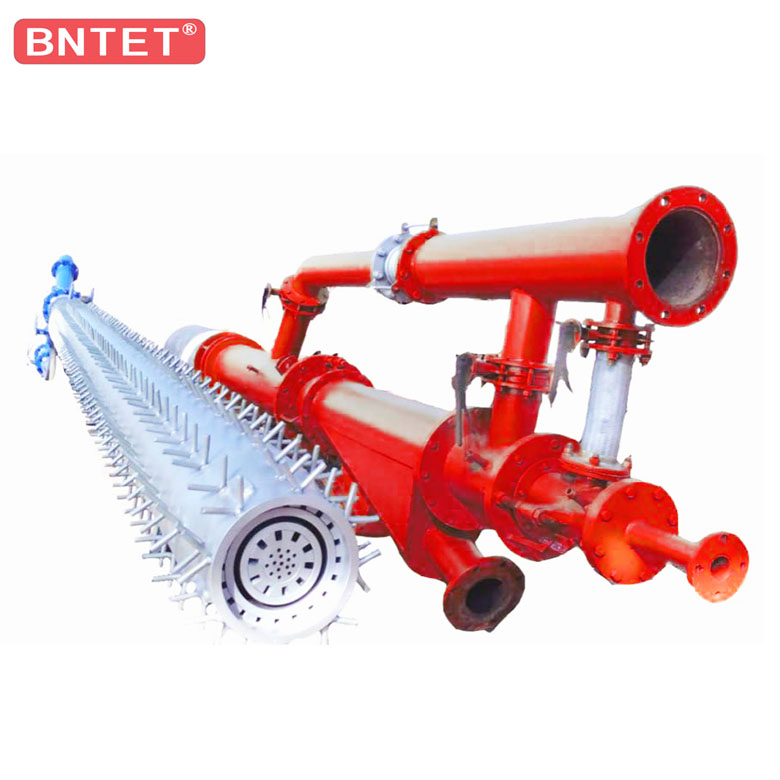
The working principle of the multi-channel burner of the rotary kiln:
Most of the burners of the rotary kiln pass through the kiln head cover, extend into the kiln head cylinder, and heat the material to the required temperature through flame and radiation. Burners have various forms such as coal injection pipes, oil spray guns, gas nozzles, etc., depending on the type of combustion. Let's learn more about the working principle of the rotary kiln burner?
The working principle of the rotary kiln burner:
When the reaction temperature is low, a combustion chamber is set beside the kiln head cover to pass hot flue gas into the kiln to supply heat. In the early days, the burners in the rotary kiln mostly adopted a single air duct structure. The primary air volume accounted for about 20%-30% of the total combustion air volume, and the primary air speed was 40-70m/s. Its function was mainly to transport pulverized coal, mix coal and air, The secondary air suction effect is very small, the flame is also inconvenient to adjust, and it is difficult to meet the production requirements. With the development of pre-decomposition technology and the increasingly stringent requirements for the use of low-reactivity fuels and environmental protection, burner technology has also made new developments.
The multi-air duct burner has the following functions:
(1) Increase the mixing of pulverized coal and combustion air, increase the combustion rate, and the fuel will burn completely and stably.
(2) Increase the means of adjusting the air volume and wind speed of each channel to make the flame shape and temperature adjustment flexible and convenient, which is suitable for clinker calcination.
(3) The burner has a long service life.
(4) Protect the kiln lining material and prolong the service life of the lining.
(5) Stabilize clinker quality and increase system output.
(6) Simple structure, convenient maintenance and replacement, reducing the operating time of the system due to burner failure.
(7) Minimize the amount of primary air, increase the use of high-temperature secondary air, and increase the utilization rate of the heat recovered by the clinker.
(8) The system resistance is as low as possible to reduce the power consumption of the primary fan.
(9) It can reduce the emission of harmful substances (especially NOx) most.
(10) Low-grade fuels can be used to strengthen the comprehensive utilization of fuels, and lower equipment prices and maintenance costs.
The above is the whole content of the working principle of the rotary kiln burner. The flame temperature of the burner part is above 1800℃, and the temperature changes frequently and the temperature difference is large due to the influence of fuel combustion. The burner lining is severely eroded and corroded by the radiation of high-temperature clinker above 1400°C and clinker dust, as well as chemical corrosion caused by the adhesion of fine-grained clinker and the alkali-sulfur compounds in the high-temperature flue gas.