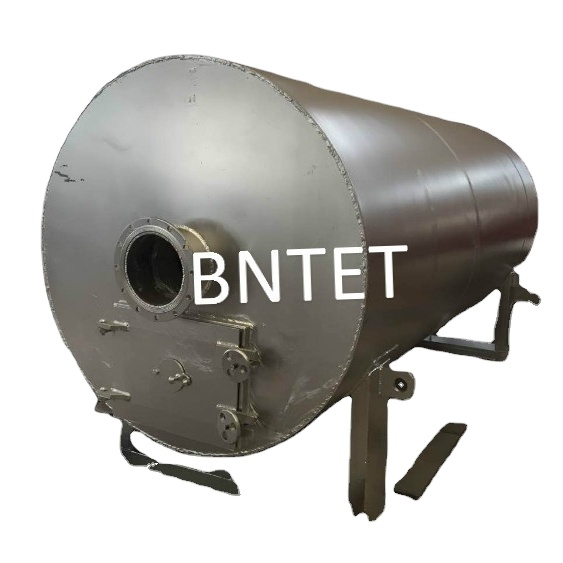
The hot blast stove is one of the very important technologies developed during the industrial revolution, because the hot blast in the hot blast stove refers to the preheating of the air blown into the blast furnace or other metallurgical processes, which greatly reduces fuel consumption. The hot air also allows for a higher furnace temperature, thereby increasing the furnace capacity.
Hot blast stoves can be mainly divided into direct hot blast stoves and indirect hot blast stoves.
The direct hot blast stove uses fuel to burn directly, forms hot blast through high purification treatment, and directly contacts the material for heating and drying or baking. The fuel consumption of this method is about half that of using steam or other indirect heaters. Therefore, the direct hot blast stove can be used without affecting the quality of the dried product. The fuel can be divided into: ① Solid fuel, such as coal and coke. ② Liquid fuel, such as diesel, heavy oil ③ Gaseous fuel, such as coal gas, natural gas, liquid gas. The high-temperature combustion gas obtained after the combustion reaction of the fuel is further in contact with the outside air, mixed to a certain temperature, and directly enters the drying room or baking room, and contacts the material to be dried, heating and evaporating water, thereby obtaining a dried product. In order to utilize the combustion reaction heat of these fuels, a set of fuel combustion equipment must be added. Such as: coal burners, oil burners, gas burners, etc.
The indirect hot air stove is mainly suitable for drying materials that are not allowed to be contaminated, or for drying heat sensitive materials with lower temperature. Such as: milk powder, pharmaceuticals, synthetic resins, fine chemicals, etc. This kind of heating device uses steam, heat transfer oil, flue gas, etc. as carriers, and heats the air through various forms of heat exchangers. The most essential problem of indirect hot blast stove is heat exchange. The larger the heat exchange area, the higher the heat conversion rate, the better the energy saving effect of the hot blast stove, and the longer the life of the furnace body and heat exchanger. Conversely, the size of the heat exchange area can also be identified from the flue gas temperature. The lower the flue gas temperature of the hot blast stove, the higher the heat conversion rate and the larger the heat exchange area.
Through the above description, I believe everyone has a deeper understanding of the hot blast stove. If you have any questions, please call our consultation hotline!