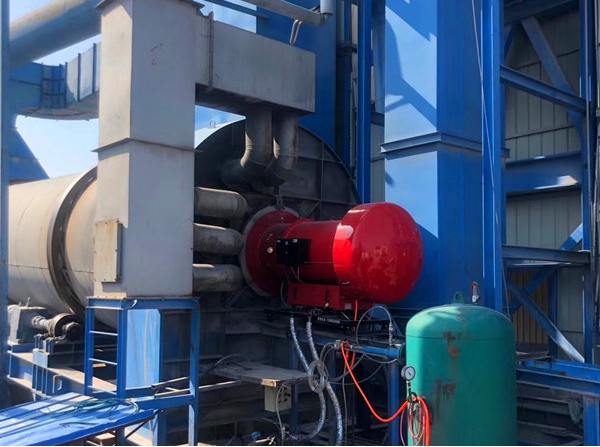
Pressure dispatch valve Check the fuel pressure regulating valve or pressure reducing valve on time, and check whether the lock nut on the dispatch bolt is clean and can be disassembled. If the screws or nuts are dirty or rusty, the dispatch valve needs to be repaired or replaced. Oil pump punctually check whether the sealing equipment of the oil pump is intact and whether the internal pressure is stable, and replace the damaged or leaking sealing equipment. When using hot oil, check whether all the oil pipes are insulated. The filter between the oil tank and the oil pump of the asphalt mixing plant burner equipment must be cleaned on time and checked for excessive wear. This can ensure that the fuel reaches the oil pump from the oil tank smoothly and reduce the possibility of potential component failure. The "Y" filter on the incinerator should be cleaned frequently, especially when heavy oil or residual oil is used, to prevent the fuel injector and valve from clogging. During operation, check the pressure gauge on the incinerator to see if it is within the normal plan.
For incinerators that require compressed air, check the pressure equipment to see if the required pressure is generated in the incinerator, clean all the filters on the supply pipeline, and check for leaks in the pipeline. Check whether the inlet protection equipment on the incineration and atomizing air blower is correct, and whether the fan shell is not damaged or leaking. Query the operating status of the blades. When the noise or vibration is too large, the blades can be dispatched to eliminate them. For the blower driven by the belt pulley, lubricate the bearing and tighten the belt punctually, acknowledging that the blower can generate extra pressure. Clean and lubricate the air valve connection to see if the operation is smooth, and replace the accessories when the operation is obstructed. Determine whether the wind pressure meets the requirements of the operation. If the wind pressure is too low, it will cause backfire, which will cause the guide plate at the front of the drum and the material plate in the incineration zone to overheat. The fuel injector should be cleaned on time and check the spark gap of the incineration electrode (about 3mm). Always clean the flame detector (electric eye), confirm whether the orientation of the device is correct, and whether the temperature is suitable. If the orientation is not correct, and the temperature is too high, the photoelectric signal will be unstable and even the fire will be broken.