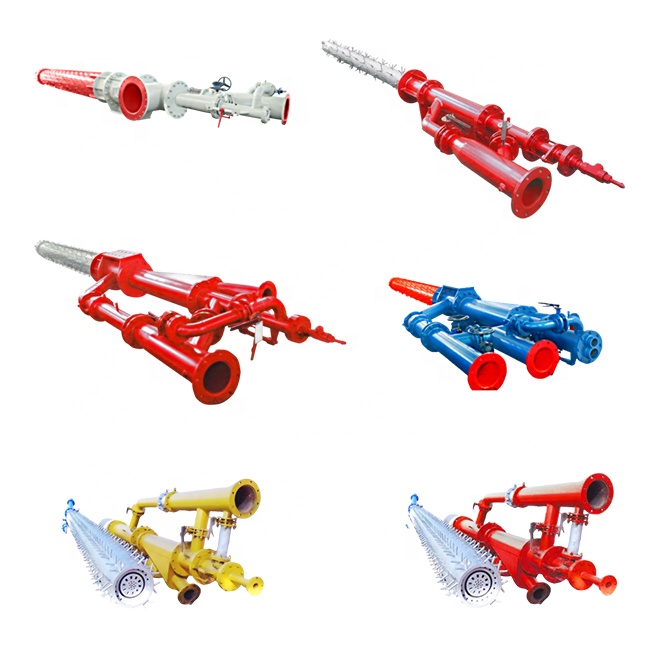
Advantages of industry cement multi-channel rotary kiln burners
The multi-channel rotary kiln burner is a new generation burner specially designed for different kiln types, different fuel characteristics and different process conditions using international advanced technology.
The multi-channel rotary kiln burner is a new generation burner specially designed for different kiln types, different fuel characteristics and different process conditions using international advanced technology.
In the cement production process, the heat required for calcination comes from the high temperature generated by the combustion of the fuel. In order to increase the output of the rotary kiln, extend the service life of the kiln lining, and expand the application range of fuels, Zhengzhou bona heat Energy Equipment Co., Ltd has done a lot of research, investigation and development work on the combustion performance of each fuel and the corresponding burners. The burner has evolved from the early single-channel burner to today's multi-channel burner. Of course, the theory and parameters of the product are mature and stable, but their use effects are different. The specific performance is that the same specifications and models of burners have different effects on the same rotary kiln from different manufacturers. The same industrial analysis may occur. The value of fuel will still fail to achieve the same effect. The main reason for this phenomenon is the adaptability of the burner design parameters to the working conditions of the rotary kiln. What are the characteristics of the multi-channel burner?
1. Long service life of the product: the use of special materials at the nozzle can achieve anti-oxidation effect at a high temperature of 1200℃; at the same time, the entrance is protected by a wear-resistant ceramic layer, which can limit the erosion of the combustor by pulverized coal.
2. Flexible online adjustment: The head section uses a stepless adjustment mechanism to facilitate online and flexible adjustment of flame strength and shape, improve operational adaptability, reduce the amount of primary air, effectively reduce nitrogen oxide emissions, and increase the service life of the kiln lining.
3. The fuel utilization rate is better, the adaptability is stronger, and the combustion efficiency is higher;
4. New energy-saving and environmentally friendly products, lower pollutant emissions;
5. It can not only realize the combustion of a single fuel to meet the thermal requirements of the system, but also use a variety of fuels to combust.