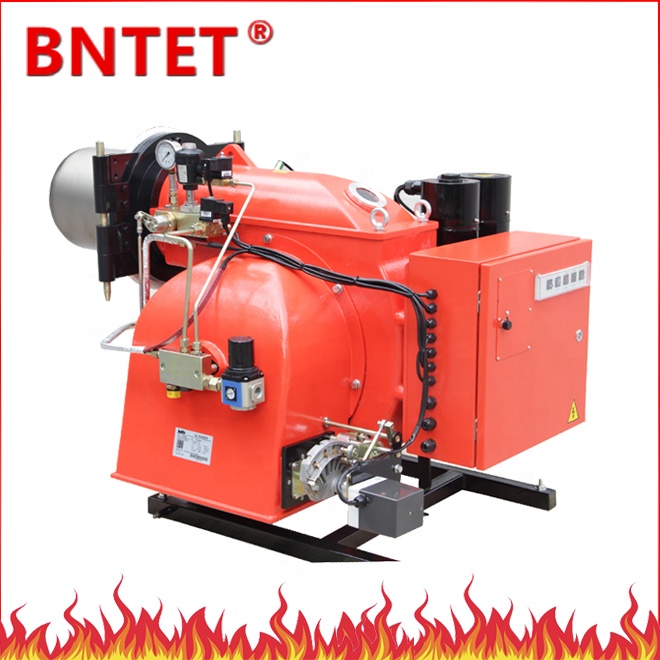
Principle: Heavy oil enters the burner in two ways, swirl oil and axial flow oil, similar to the internal and external wind of the burner. Swirl oil is distributed in a circular shape on the outside; axial flow oil is a straight cylindrical jet in the middle. When it reaches the head of the spray gun, it converges into a road and enters the kiln through the nozzle hole of the atomization plate. The atomization plate is divided into a variety of specifications according to the size of the nozzle hole. In the process of heating up and feeding, change the atomizers of different specifications as needed.
Product use: Heavy oil is a by-product of crude oil after refining. It is generally prepared from cracked heavy oil, vacuum heavy oil, atmospheric heavy oil or wax oil in different proportions.
When selecting, the overall requirements should be high calorific value, good combustion performance, moderate viscosity, small corrosiveness and solid impurities, and easy to store and transport.
Viscosity indicates the flow performance of the fuel. The higher the viscosity, the worse the atomization effect. It is the most important quality index and service performance index of heavy oil, which directly affects the working efficiency and fuel consumption of fuel pumps and fuel injectors. With the increase of temperature, the viscosity of heavy oil gradually decreases. Therefore, the oil with high viscosity must be heated and increased in order to be transported and atomized smoothly.
Therefore, when selecting oil, in addition to understanding the conventional indicators of the oil, it is also necessary to understand the viscosity-temperature curve of the oil to ensure that the heating can make the heavy oil reach the viscosity required by the burner before atomization. For mechanical atomizing burners, the best fuel viscosity in front of the nozzle is 2.5-3.5°Et, and the best fuel viscosity of high-pressure air atomizing burners is 4.5-5.8°Et.
The unit of viscosity is expressed by Engel's viscosity (°Et) and kinematic viscosity νt (mm2/s, also called centistokes cSt). The conversion relationship is: νt=7.310°Et-6.31
Product advantages:
1. The flame stabilizer is used to maintain a stable vortex circulation at the root of the flame and reduce the rotation of the internal air, so that the primary air volume can be reduced by half.
2. A flame holding hood is used to prevent the heavy oil entrained in the airflow from diverging arbitrarily to produce a brake-like effect.” The flame shape history is reasonable to avoid the high temperature of the kiln head and prolong the service life of the kiln head guard iron.
3. The external clean air has an intermittent rectangular straight air jet, and it is changed to an annular gap jet after reaching the front of the burner. At the same time, the area of the annular gap is increased to lengthen the flame and increase the average temperature in the kiln.
4. Swirl blades are installed at the front end of the inner air duct, 2cm away from the front end of the outer air cylinder wall, to play the role of gathering the flame and avoid the high temperature of the kiln head. The first handle of the burner can be adjusted. The position of the swirling blade is located at the 6” position of the scale when it leaves the factory. The adjustment range is 0} 6cm. There is no negative value. The internal wind swirl can only be pulled back to lengthen the flame.
5. The center wind blows the high-temperature gas around the nozzle and pushes it back, which not only cools the interior of the nozzle, but also cools the end face, thereby protecting the burner head and prolonging the life of the burner.