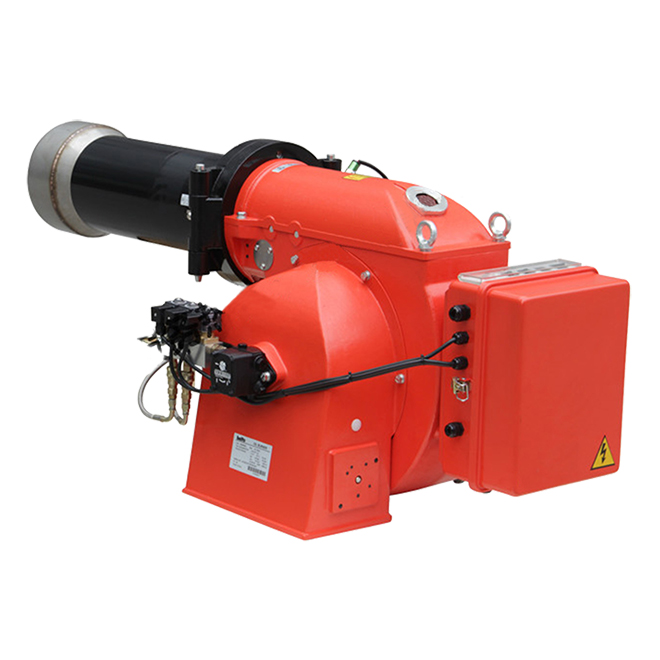
Linde, in cooperation with Hertwich AG and Corus Aluminum, jointly developed a Tilting Rotary Furnace (URTF) that meets the needs of the secondary aluminum industry. This new furnace type has improved production efficiency and metal output through excellent process control, while reducing energy consumption. Furnace tonnage is available from 5 to 20 tons, melting rate is 1 to 5t/h, and natural gas consumption per ton is about 25m3 to 45Nm3. Molten salt consumption is also greatly reduced.
In order to achieve the best transformation from air combustion to pure oxygen combustion, the existing production process and system control need to be adjusted or optimized accordingly. The amount of flue gas produced by air combustion is more than three times that of pure oxygen combustion. Therefore, after the transformation of pure oxygen combustion technology, the flue gas pipeline and exhaust fan must be designed and optimized accordingly, such as reducing the fan power and flue size. After converting to oxy-fuel combustion, the furnace pressure parameters need to be re-checked to ensure that they are in the best range required by pure oxy-fuel combustion technology. If the flue gas system is not modified, when the new pure oxy-fuel combustion system is activated, the power of the original exhaust system is already too large, which will cause cold air to be sucked into the furnace. Once this happens, it will have a serious negative impact on the melting effect after transformation. A pure oxy-fuel burner with a bright flame produces a flame with a higher flame temperature than an air-burning flame. Therefore, it is best to install a thermocouple in the melting furnace to prevent the refractory from overheating when performing pure oxygen combustion technology transformation. When choosing a pure oxygen combustion system, special attention should be paid to the need to carefully select the size and shape of the flame to match the size of the furnace. If the choice is improper, a too short pure oxy-fuel combustion flame may generate high temperatures locally and cause the furnace temperature to be too high. Too long a pure oxygen combustion flame will seriously wash the refractories of the furnace or damage their mechanical parts. The length of the flame needs to be adjusted to meet the specific furnace size, and the combustion process should be optimized to meet the needs of raw materials and melting process conditions. The German Linde Group has established pure oxy-combustion technology experimental centers in Europe, the United States and China. R&D personnel have developed a series of combustion technology solutions for non-ferrous metal industrial applications. In general, the effect can be summarized as: increase melting efficiency up to 50%; save fuel up to 50%; reduce aluminum burning loss and scum formation; reduce carbon dioxide emissions up to 50%.